Gen 3 Wall Connector Tester
GCM
Overview
As a power electronics engineer, I played a pivotal role in architecting an intricate test system for Tesla’s Gen 3 Wall Connector. My expertise in power electronics drove me to understand the electrical functionality of the wall connector intimately. Besides curating specialized electronic tests, I also spearheaded the mechanical design process, stretching my responsibilities from CAD conceptualization, and meticulous drawing drafting, to supplier management and procurement.
Collaborations & Achievments
- Undertook a deep dive into the SWC (Signal Word Code) debugging, ensuring that the Wall Connector’s software interfaced perfectly with its electronics.
- Conceived, executed, and refined a broad range of test protocols based on a profound understanding of the wall connector’s electrical functionality.
- Managed the mechanical design process singlehandedly: originating CAD designs, producing detailed drawings, and advancing to the final prototype stages.
- Built and maintained strong relationships with suppliers for the timely and efficient procurement of components.
- Exercised comprehensive oversight over the project, from mechanical design, test protocols, to SWC debugging, leaving only the electrical schematics to fellow specialists.
- Fostered collaborations with firmware teams, wireless experts, and hardware colleagues to create an integrated testing approach that encompassed all facets of the product.
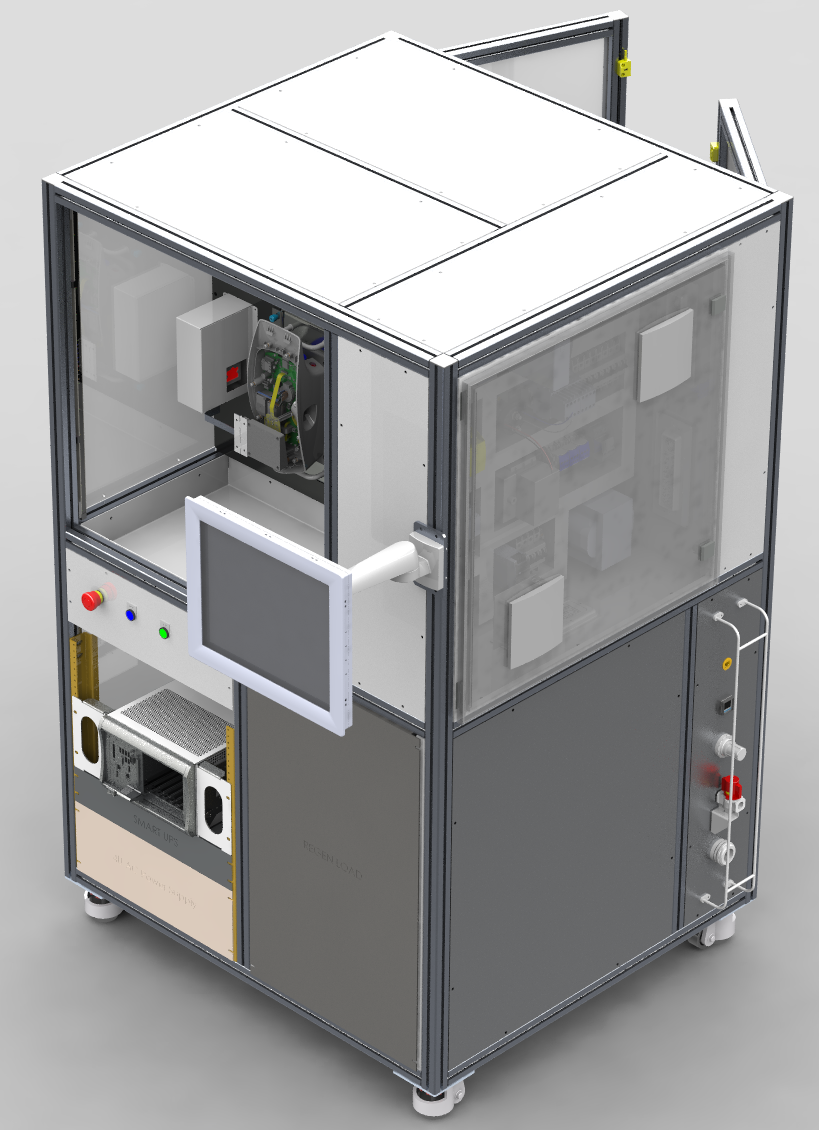
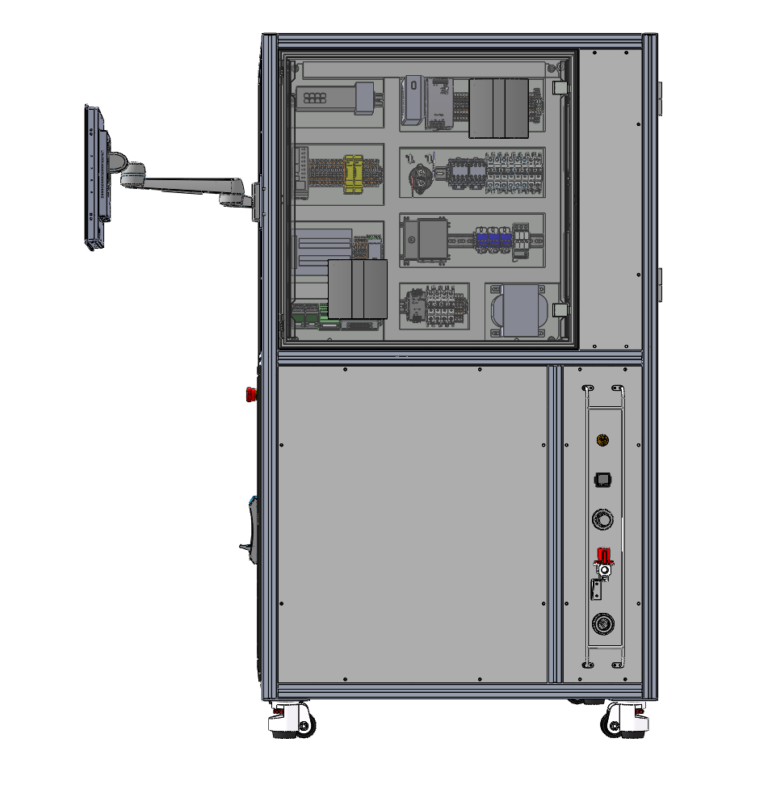
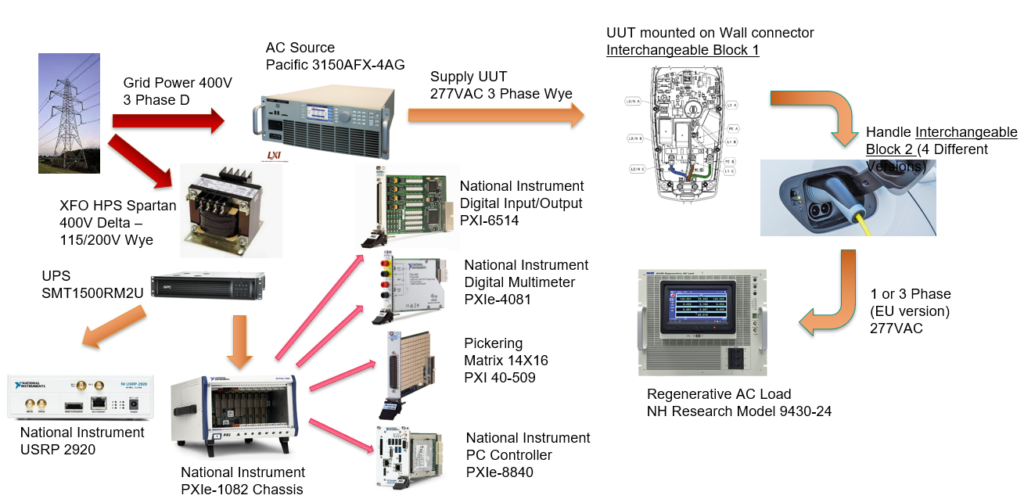
Key Features
- Resistance Test:
- Objective: Evaluate the internal resistance of the Wall Connector, ensuring optimal energy flow and reduced losses.
- Developed protocols to connect test points to a resistance meter, apply specific current levels, and monitor results across varied test scenarios.
- Hipot Test:
- Objective: Ensure that the Wall Connector can handle potential over-voltage conditions without breaking down.
- Designed procedures to apply elevated voltage levels and validate the connector’s insulation strength and breakdown resistance.
- Insulation Resistance:
- Objective: Validate the insulation robustness between the connector’s different components.
- Devised a testing methodology employing an insulation resistance tester to meet specific insulation parameters, guaranteeing protection against unintentional current paths.
- Functional Test:
- Objective: Comprehensive evaluation of the Wall Connector’s assembly, firmware, and functional attributes.
- Created sub-tests, covering firmware updates, pilot circuit functionality, PLC circuit assessments, and more, with clear parameters, procedures, and criteria.
- Zero Current Burn-In:
- Objective: Verify the Wall Connector’s sustained performance.
- Strategized an approach involving real-time interactions with a Vehicle Simulator, providing consistent monitoring and management of voltage dynamics.
- Leak Test:
- Objective: Ensure water ingress protection.
- Formulated a test environment to maintain specific pressures and monitor for potential leaks, ensuring long-term durability in various environmental conditions.
- Additional Tests:
- Developed further tests like UHF Transmission for energy metering accuracy, WiFi & NFC checks for wireless capabilities, and Energy Metering Calibration for precise energy transaction measurements.