Designing for Complex Manufacturability and Assembly
GCM
Portable Milling Unit for Edge-Case Medical Robot Manufacturing
Engineered a portable milling unit to automate a previously manual, hour-long machining process, reducing cycle time to 10 minutes. Conventional CNC machines were incapable of handling the precision and constraints required for edge-case medical robotics manufacturing, necessitating a custom solution.
Key innovations included:
- Custom Miter Bearing System & Motor Controls: Designed a high-precision miter bearing assembly to handle complex force distributions, ensuring low backlash and high durability under repeated load cycles. Integrated motor-driven automation for consistent, repeatable performance.
- Material Selection & Coatings: Utilized hardened tool steel for structural integrity and wear resistance, coated with diamond-like carbon (DLC) and PVD coatings to minimize friction, enhance tool life, and prevent material adhesion.
- Magnetic Lifting Mechanism for Part Loading: Developed an integrated magnetic lift system, allowing secure and precise part positioning without clamps, improving workflow efficiency and minimizing setup time.
- Modular, Portable Design: Engineered the system in separate, lightweight steel and aluminum sections, enabling easy transport and assembly without sacrificing rigidity or precision.
Led the full electrical and mechanical design, including sensor integration, real-time motor control tuning, and custom electrical enclsoure. This solution successfully achieved precision machining where conventional CNC systems failed
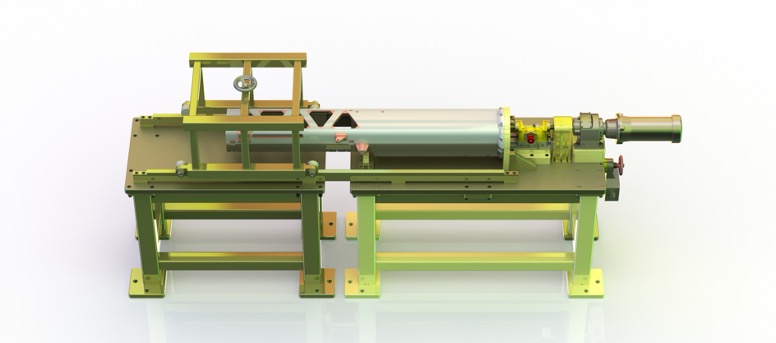
High-Precision Robotic Welding Fixture for Multi-Process Integration
Engineered a robotic welding fixture designed to handle tolerance stack-ups while maintaining precision GD&T control within 0.001 inches. This system allowed for the seamless integration of multiple robotic welding processes into a single automated workflow, improving efficiency and reducing production variability.
Key innovations included:
- Precision GD&T & Tolerance Management: Designed for extreme accuracy (±0.001″), ensuring repeatable part positioning and compensating for stacked tolerances across multiple components.
- Multi-Process Welding Integration: Enabled multiple robotic welding operations to be performed within one fixture, reducing rework, part handling, and cycle time.
- Simulation & Optimization: Ran FEA and welding deformation simulations to ensure structural integrity and distortion control, validating the design for thermal expansion and load-bearing capacity.
- DFM & DFA Principles: Optimized the fixture for manufacturability and assembly, utilizing modular construction and self-locating features to simplify setup and minimize variation.
- Material & Coating Selection: Utilized hardened tool steel with high-wear coatings (e.g., DLC, nitriding) to withstand high thermal loads and repeated fixture cycles.
Led full mechanical design, simulation, and validation, ensuring scalability for high-volume production while maintaining precision and consistency in robotic welding automation.
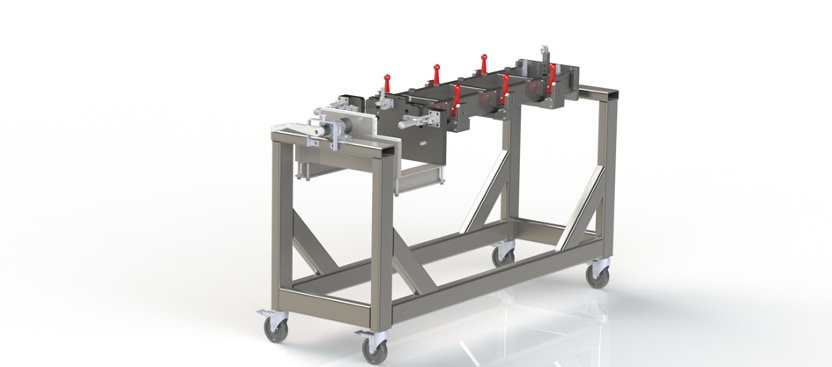