Cosmetic Inspection System
GCM
Overview
The idea of this project was created in February 2023 after doing an analysis of our scrapped and reworked parts. It was determined to lift a $2M financial burden if we could image our parts for hardware detection and eventually cosmetic defects as well as send our customers a document of inspection. In the future, we hope to develop numerous of systems for each of our facilities.
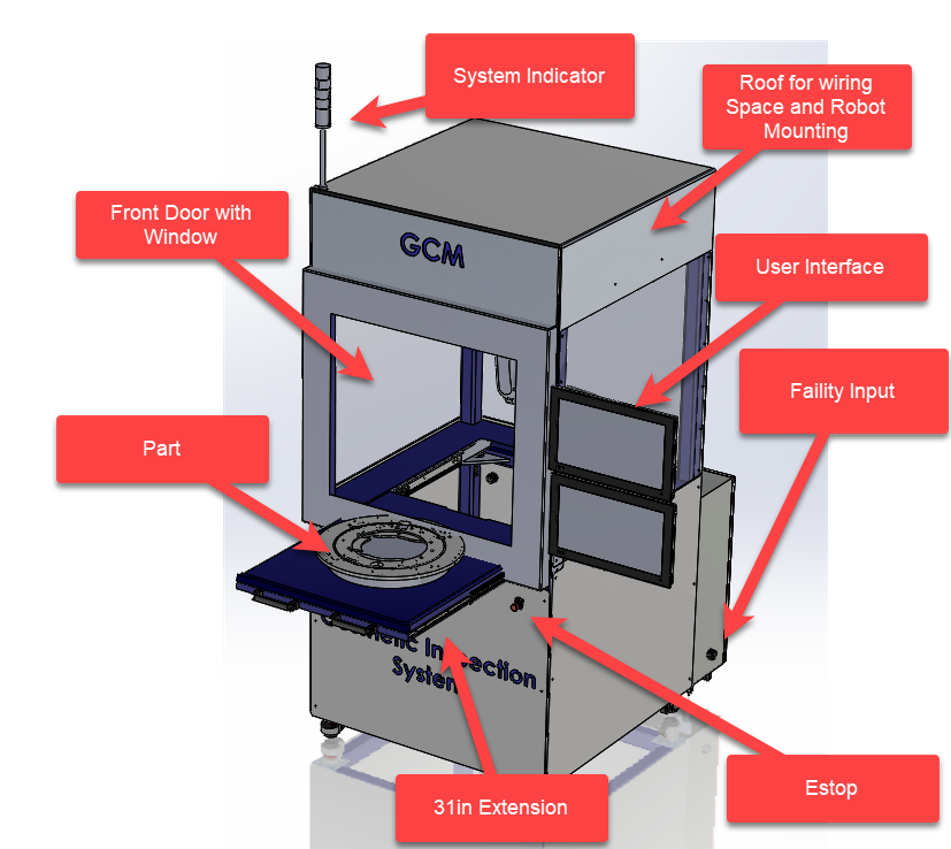
Project Description
This project’s purpose is to design a system to caption cosmetic defects on our parts. The cosmetic defects consist of:
- Scratching (20-100micron)
- Any cosmetic defect that can be detected by the eye (i.e fingerprints)
- Hardware (i.e helicoils)
- Serial Number/Barcodes
- Hole Dimensions
The largest part for this system is around 750mm. The system should pass all necessary risk assessments.
A Steel tube frame will be manufactured with sheet metal paneling. The base in which a part is placed should be adjustable and able to be moved out of the frame by the user when replacing parts. Two screens and a keyboard should be mounted to the frame for the user interface. The electrical enclosure will be connected to the steel frame. The base plate should be at an ergonomic height for standing users. A robotic arm will be vertically mounted to the steel frame for the motion control of the Camera. The mount for the robotic arm should have leveling and dampening capabilities. Vibration should be dampened from external forces to the frame as well as from the robotic arm. The user entry door has a safety locking feature while the robot is inspecting parts. See Mechanical design, fabrication, and assembly proposal. The user interface allows a user to switch between parts which will detect all or some of the described defects depending on the desired inspection for the part. When a defect is detected, this is to be shown on a screen next to an image of the entire part mapping the defect to the specific location on the part (see user interface for more details). At the end of the inspection, the images that were taken on the part are loaded into our custom PDF document with the number of fails. If at any time our safeguarding or Estop is triggered, the system stops. Any error from the Robotic Arm, Camera, or user will be displayed on the user interface with the proper available actions. Additionally, it is easy for GCM employees to upload environments for new parts to the system. For example, we should be able to upload a CAD-CAM path and program Camera Scenes for new parts so the user can select these parts for inspection.
User Interface
The user interface allows a user to switch between parts which will detect all or some of these defects depending on the desired inspection for the part. When a defect is detected, this is to be shown on a screen next to an image of the entire part mapping the defect to the specific location on the part. At the end of the inspection, we would like the images that were taken on the part to be loaded into our custom PDF document with the number of fails. If at any time our safeguarding or Estop is triggered, we would like to stop the system. Any error from the Robotic Arm, Camera, or user should be displayed on the user interface with the proper available actions. Additionally, it should be easy for a GCM employee to upload environments for new parts to the system. For example, we should be able to upload a CAD-CAM path and program Camera Scenes for new parts so the user can select these parts for inspection. There should be a user log in, we have a REST API that can be imported, or users can be manually entered in.
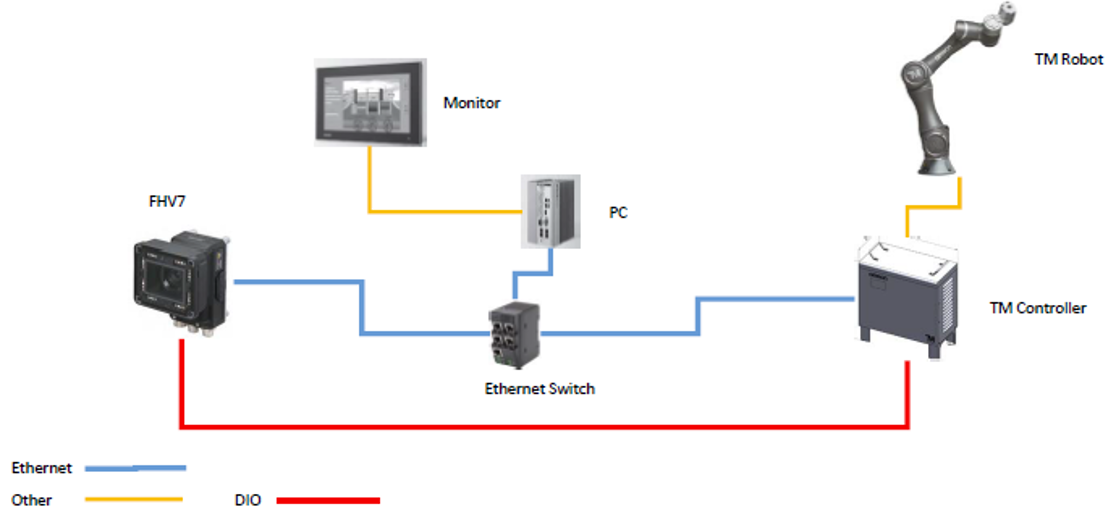
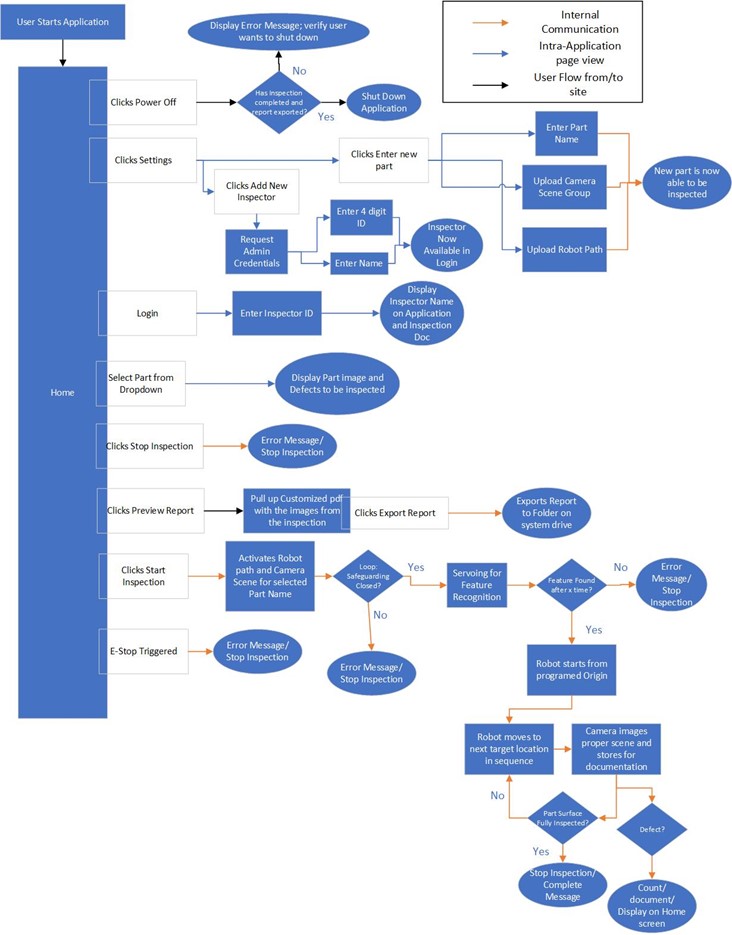