52 Kw DC/DC Converter
Tesla
Overview
At a critical juncture of Tesla’s ambitious expansion into fast-charging infrastructure, I was entrusted with the responsibility of designing and developing the mechanical components for a 52 kW DC/DC Converter Testing System. This system is instrumental in ensuring the performance and reliability of Tesla Superchargers.
Collaborations & Achievments
- Supplier Collaboration: Recognizing the importance of sourcing the right materials and components, I fostered close collaborations with suppliers, ensuring timely procurement without compromising on quality.
- Interdisciplinary Coordination: Working on such a multifaceted project demanded close coordination with electrical engineers, firmware teams, and manufacturing specialists. My role often served as a bridge, ensuring the mechanical designs were in harmony with electrical requirements and manufacturing capabilities.
- Project Realization: The end result was a robust, efficient, and scalable testing system that now plays a crucial role in vetting and validating Tesla Superchargers before they’re deployed in the field.
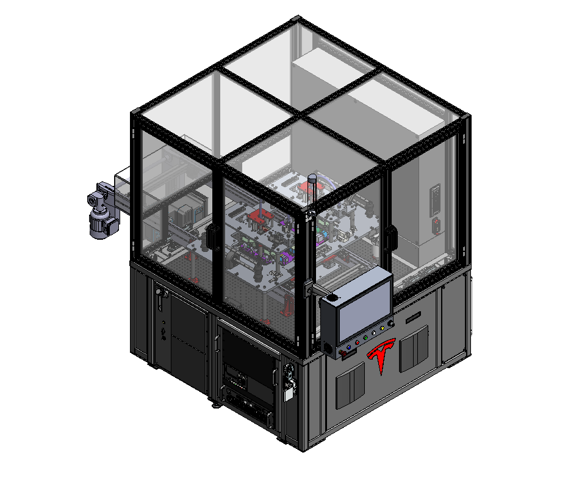
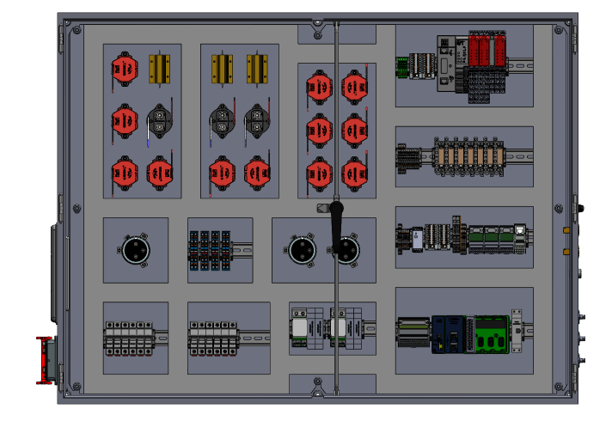
Key Features
- Electrical Panel Design: I conceptualized and drafted the mechanical design for the electrical panel of the converter, ensuring optimal component arrangement for effective heat dissipation, easy maintenance, and streamlined electrical routing.
- Sheet Metal Parts Creation: Given the robustness and precision required for such a high-power application, I took on the challenge of designing various sheet metal parts. My design process prioritized both functionality (ensuring parts could withstand electrical stresses and thermal cycles) and manufacturability (ensuring ease of fabrication and assembly).
- Prototyping & Iteration: After initial designs were drafted, I closely collaborated with fabrication teams to prototype these components. This iterative process allowed me to refine designs based on real-world feedback, ensuring the final components were both cost-effective and performance-optimized.